One-Stop Additive Manufacturing Solution For Customized Automotive Needs
1.Shorten R&D cycle
2.Reduce manufacturing costs
3.Break through the formation of complex structures
4.Achieve lightweight
Innovation and development, technological innovation, so that car development and design more free, manufacturing more simple
Structural optimization, research and development, small batch production, personalized products and spare parts are several important application points of additive manufacturing in the automotive field. Structure optimization design can significantly reduce vehicle weight and fuel consumption; Development and trial production without opening mold, can shorten the vehicle development cycle from 32 months to 18 months; Mass production can realize digital manufacturing, no tooling fixture; Personalized products can be designed according to the individual needs of customers, and multiple products are produced in the same version; Spare parts manufacturing solves the problem of uncertainty and reduces capital, space and capacity.
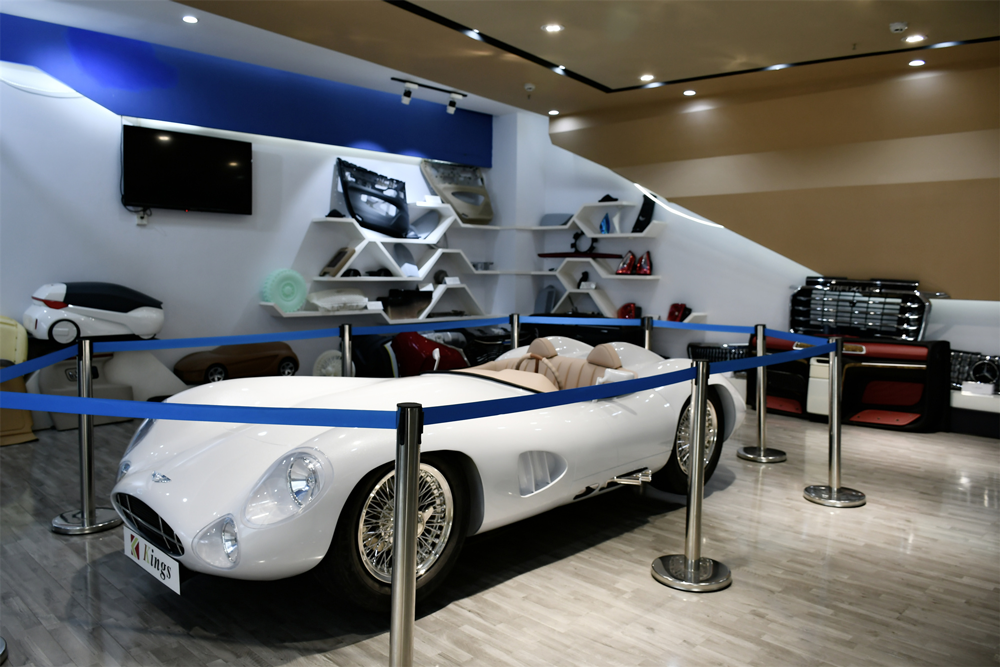
Technological Advantage
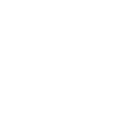
1.Optimize the structure of parts and break through the formation of complex structures
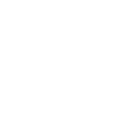
2.High quality digital production, more stable product quality, higher precision
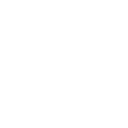
3.High efficiency mass production, shorten production cycle, improve efficiency
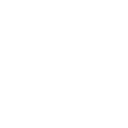
4.Lightweight structure optimization design, taking into account product performance and parts safety weight reduction
Cooperative customer
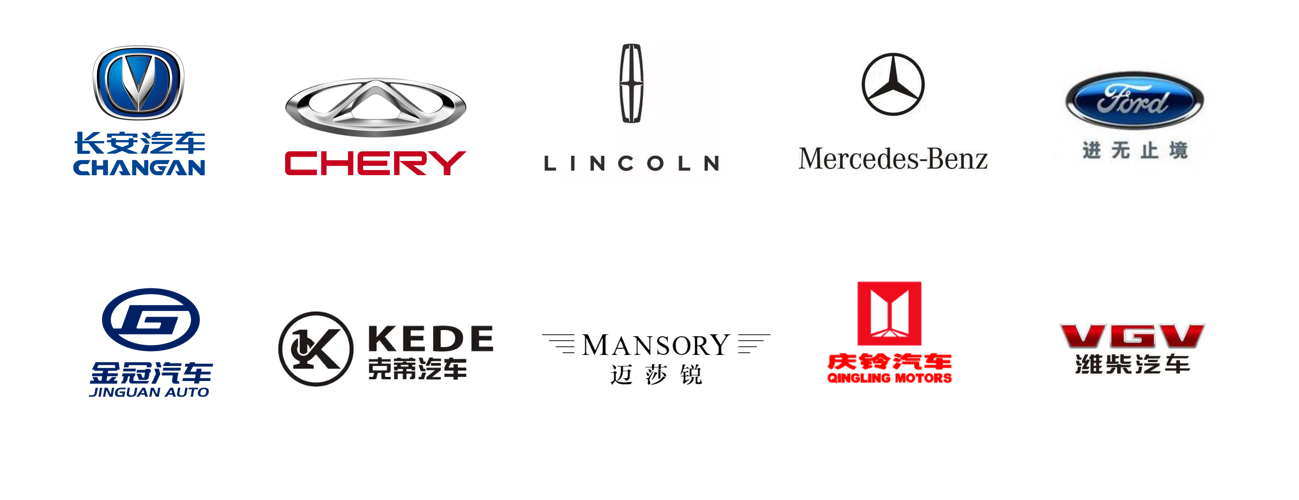
Sample Display
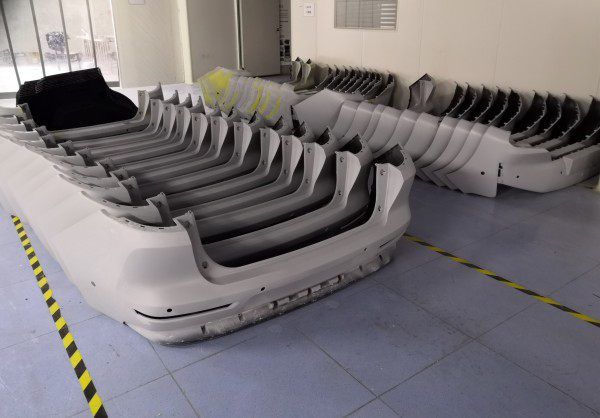
Automotive Bumper
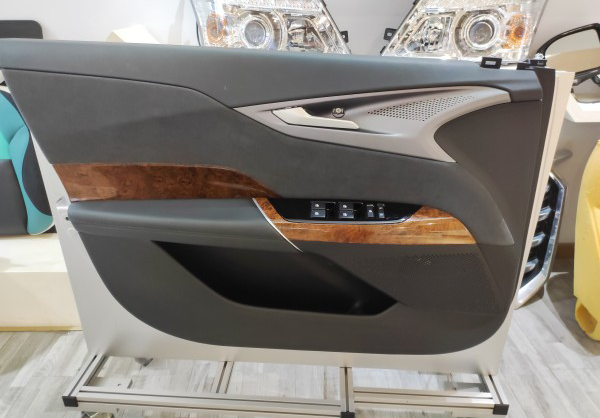
Car Door Panel
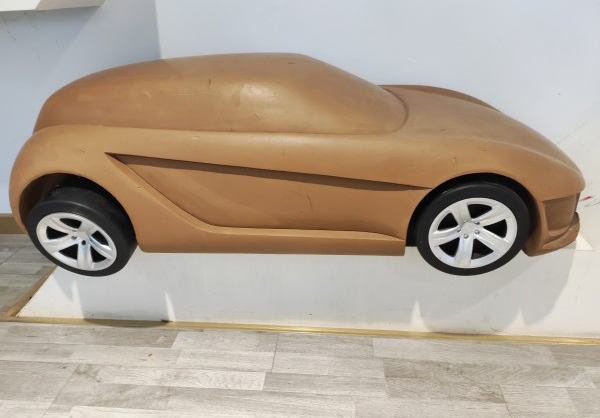
Car Mold
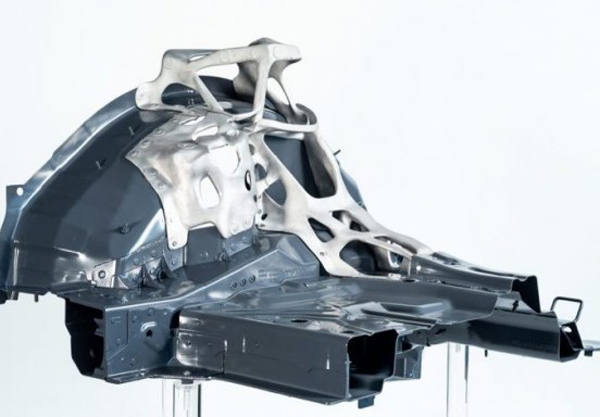
Fender Beam
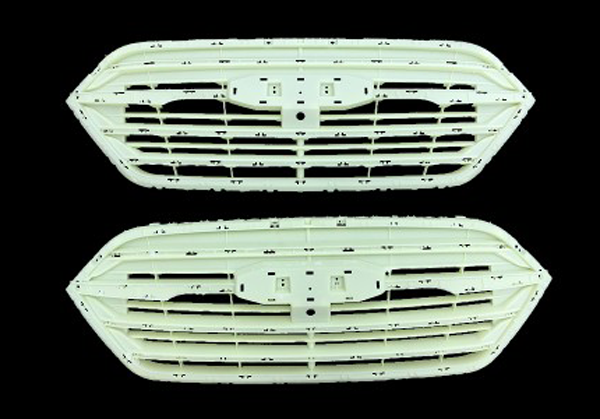
Grille
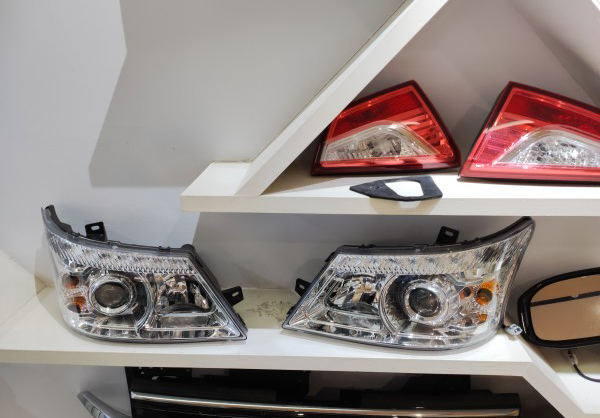
Headlight
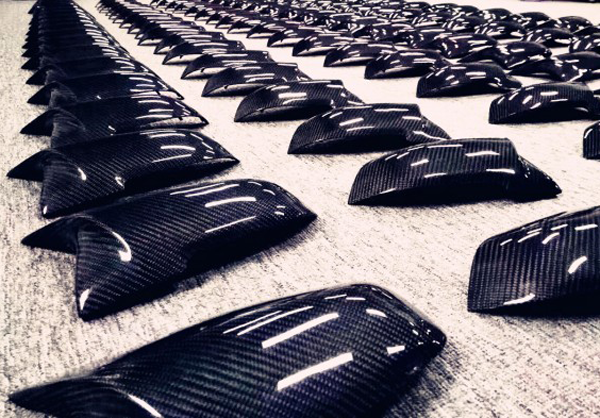
Rocker Panel
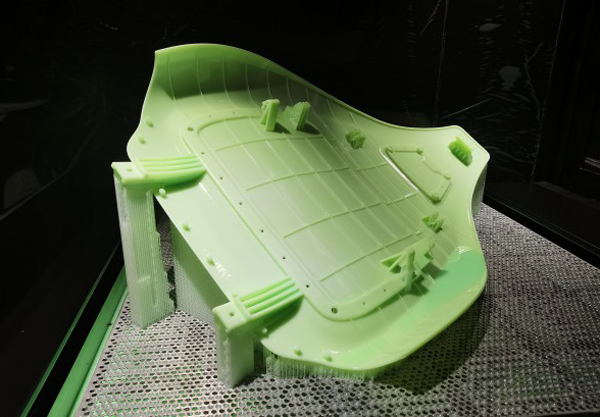
Saet Part
Item Process
1.Requirements:Provide the overall modification design scheme and the prototype design of the modified parts, modeling structure design, etc

2.Sample:Quickly produce samples through 3d printing for design verification, assembly verification, exhibition display and more

3.Small Batch:By 3d printing and silicone mold trial production of 5-200 products, test market feedback

4.Injection mold: The use of simple injection mold mass production of 200-1000 modified parts, mold cost saving 30%-70%