Selective Laser Sintering (SLS) is a powder-based 3D printing technology that uses lasers to fuse layers of material into the final part. The laser tracks the 3D design of the pattern for each cross section and replicates it onto the powder bed. After building a layer, the modeling platform descends and starts building another layer on top of the previous one. This process will continue until all layers are built and the parts are actually manufactured.
Nylon 12 Powder, Nylon 12 GF Powder, and TPU 90A Powder are all nylon 3D printing materials introduced by JS additive that can make production-grade finished parts on selective laser sintering SLS 3D printers.
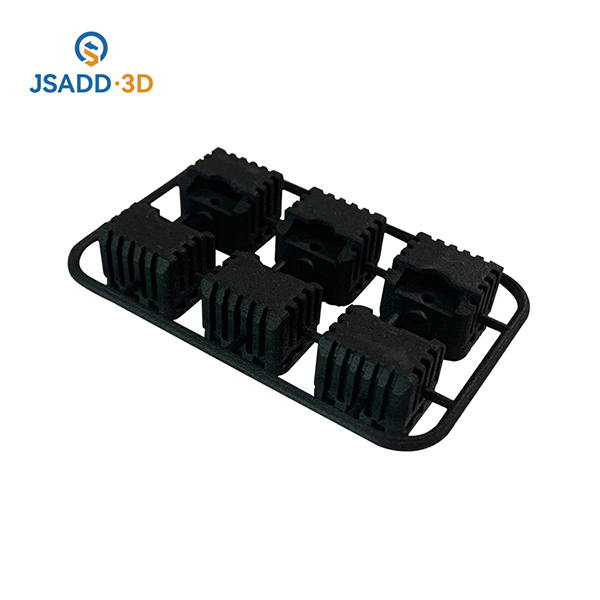
The greatest advantage of selective laser sintering technology (SLS) is the high degree of detail and strength of the components. In addition, there is no need for support structures during the 3D printing process, as the powder bed supports the components, just like in the adhesive spray. Unprinted materials can be recycled and reused up to 100%. Similar to all other 3D printing technologies, SLS is primarily used to produce prototypes. At the same time, however, many users are also producing small batches using selective laser sintering. When durable plastic parts are needed, SLS can fully show its advantages.
Whether functional or purely visual prototyping - attention to detail and the mechanical loading capacity of 3D-sintered parts, as well as the availability of many different SLS materials, have contributed to the widespread use of 3D printing technology. Particularly in the aerospace, pharmaceutical and automotive manufacturing sectors, this process is now firmly established. Even applications that go beyond classic prototypes, such as small batch production, can now be achieved economically through selective laser sintering technology.