Step 1: File Review
When Our Professional Sales receive the 3D File (OBJ, STL, STEP etc..) provided by the clients, we must first review the file to see if it meets the requirements of 3D printing. If there is any missing surface in the file, it needs to be repaired. If the customers don’t have 3D file, we need to communicate with them about it.
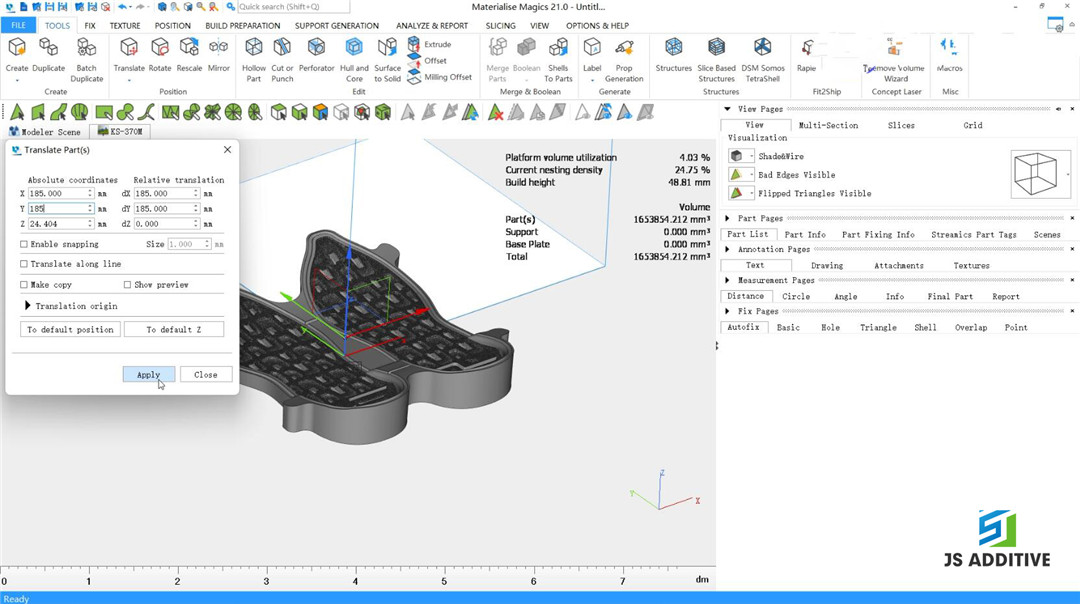
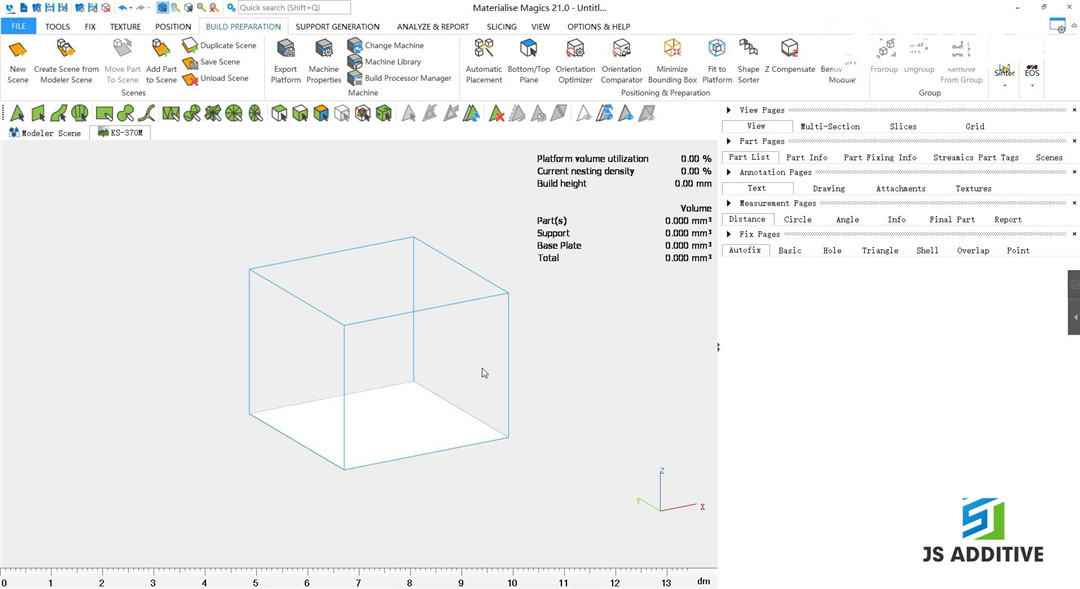
Step 2: Quotation and Confirmation
After the files is completed, we will offer a quotation based on the materials and post-processing requested by the customer. The quotation needs to be confirmed.
Step 3: Slice Programming
When the customers confirm the quotation and make the payment, we will perform 3D slicing processing on it with different layer thickness and precision according to the requirements of the customer’s industry.
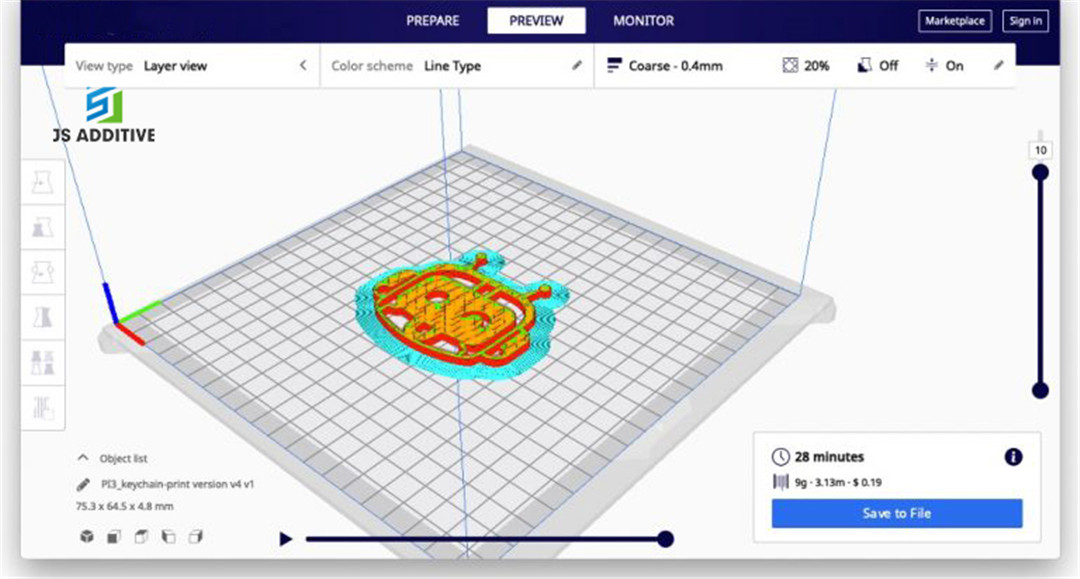
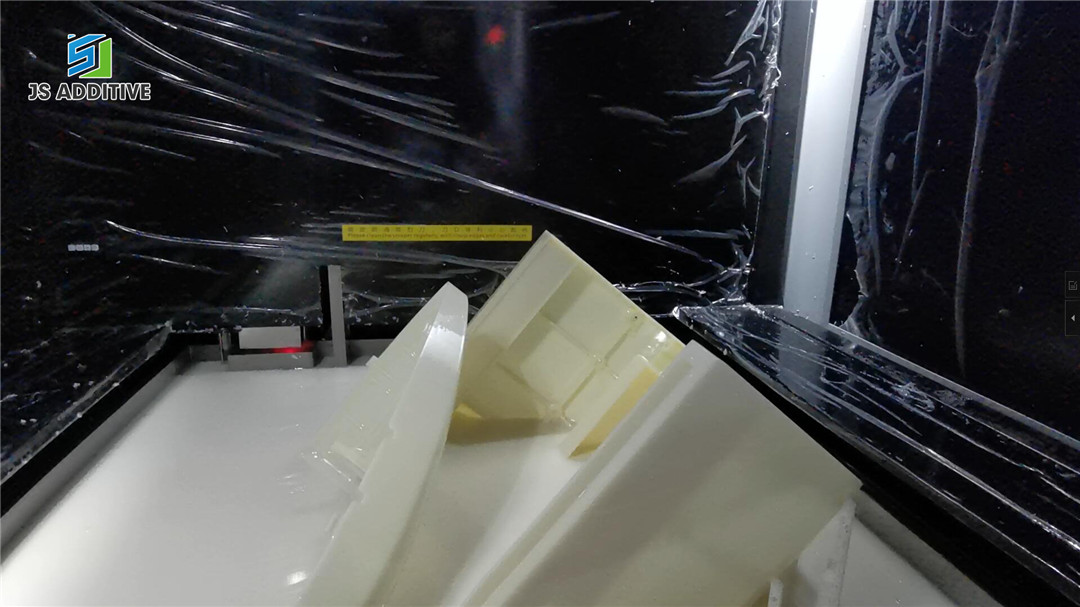
Step 4: 3D Printing
We import the processed 3D data into a high-precision industrial-grade 3D printer, and set the relevant parameters to make the equipment run automatically. Our staff will regularly inspect the printing status, so that any abnormality can be dealt with at any time.
Step 5: Post-Processing
After printing, we take out the printed product, clean it with industrial alcohol, and put it into the UV curing box for further curing. We polish it according to the needs of customers and the characteristics of the industry. We could also electroplate and paint the product if the customer demands.
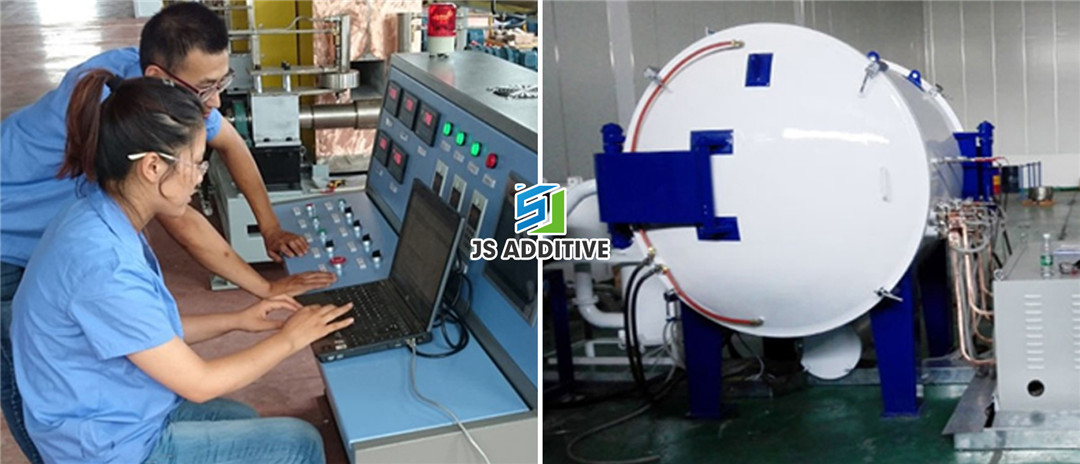
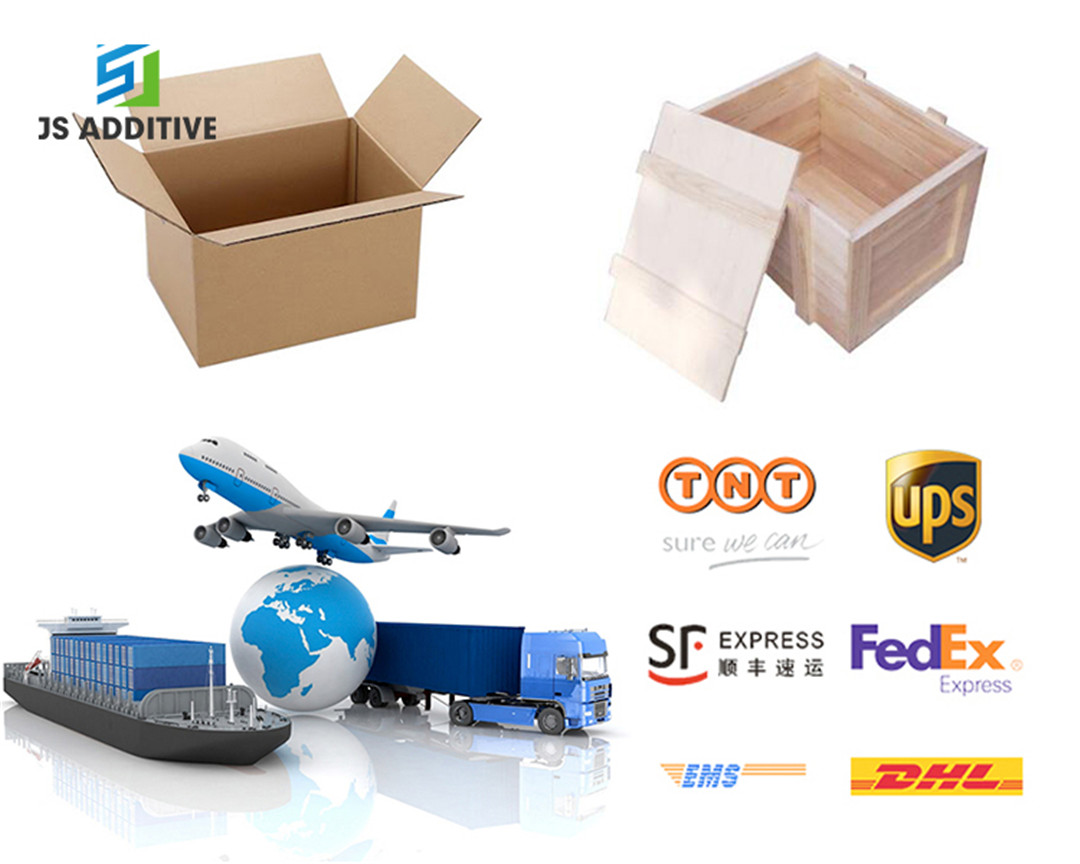
Step 6: Quality inspection and delivery
After the post-processing is completed, the professional quality inspection personnel will conduct inspection on the size, structure, quantity, strength and other aspects of the product according to the customer's requirements. If the product is unqualified, it will be processed again, and the qualified product will be sent to the customer's designated location by express or logistics.